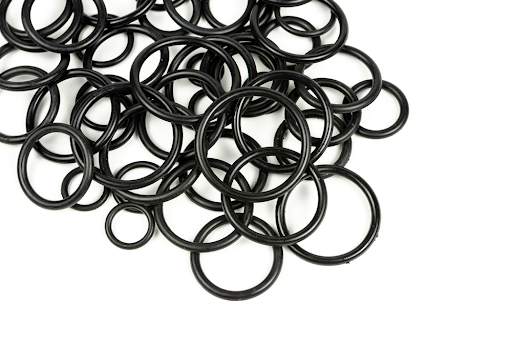
O-rings are commonly used by different industries, including aerospace, automotive, construction, medical, and oil and gas. As they are easy to install and highly effective, industries use them as hydraulic and pneumatic piston seals, rotary seals and axial seals in several static and dynamic applications.
Let’s take a look at the different materials used to make o-rings and how they can be used in a plethora of applications.
Table of Contents
Materials Used to Create Different Types of O-Rings
O-rings are fabricated using different materials, making them compatible with varied application environments. Some of the most commonly used compounds are Buna (nitrile), Viton (fluorocarbon), silicone, ethylene propylene rubber and Teflon (PTFE).
Buna: An elastomer compound, Buna is used to manufacture general-purpose o-ring seals, which offer resistance to petroleum-based fuels, lubricants, water and some hydraulic fluids. O-rings made of Buna are suitable for applications that have low resistance requirements.
Viton: This is a fluorocarbon-based compound that can handle a wide temperature range. Viton is appropriate for petroleum-based fuels, silicone fluids and gases, and chlorinated hydrocarbons, and hence, o-rings made of fluorocarbon are suitable for aircraft, automobile and chemical processing industry applications.
Silicone: Vinyl-methyl-silicone (VMQ) is usually the key ingredient of this highly flexible material. Silicone o-rings are more suitable for static applications such as fuel injection ports. It is best not to use them for dynamic applications as they offer poor abrasion resistance.
Ethylene Propylene Rubber (EPR): Prepared from ethylene and propylene monomers, EPR is an elastomer that offers excellent resistance to steam, water, silicone oils and automotive brake fluids. Hence, EPR o-rings are appropriate for hydraulic pumps used in the aerospace industry.
Teflon: Also called PTFE, Teflon is a hard plastic that is unstretchable. As Teflon maintains its strength and toughness in low and high temperatures, it is more suitable for use in static applications such as automotive steering devices and paint guns.
Neoprene: A multi-purpose elastomer, Neoprene provides good resistance to petroleum fluids, UV light and oxidation. It can seal refrigerants used in air conditioners and refrigeration units, making Neoprene o-rings suitable for air conditioning systems.
O-Rings Available in AS568 & ISO 3601 Standard Sizes
In the U.S., o-rings are available in an incredible number of different sizes, conforming to the dimension standard specified by AS568 and ISO 3601.
Published by the Society of Automotive Engineers (S.A.E.), AS568 specifies the sizes of o-rings in cross-sectional diameters (ranging from 0.040 to 0.275 inches) and inside diameters (ranging from 0.029 to 25.940 inches). There are 369 standard sizes available under AS568. ISO 3601 standard sizes, on the other hand, are issued by the International Organization for Standardization.
ISO 3601 groups metric sizes into G and A series. The former contains 445 sizes and is used for general purpose applications, while the A series is recommended for applications where tighter sealing is required, for example, applications used in the aerospace industry. There are 383 sizes in the A-series group.
Choose Only the Right O-Ring
No two applications are the same, and therefore, not all o-rings are appropriate for them. For an o-ring to perform optimally in an application, it is important to select it after determining the material used to fabricate it, its size and durometer, application temperature, sealing pressure, and lubrication requirements.
Originally posted 2022-04-06 21:00:45.
Hello, I am a professional writer and blogger at Adclays.com. I love to explore the latest topics and write on those topics. I spend the maximum of my time on reading and writing interesting topics which provide valuable piece of information to my readers whether it comes to the latest fashion, technology, healthy lifestyle, business information, etc. Explore my writings by visiting the website.