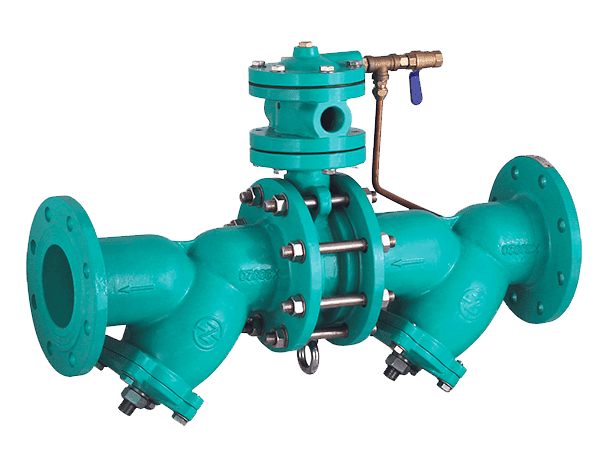
A backflow preventer is a critical device that allows water to flow in one direction only and prevents your drinking water and the city water supply from mixing in with contaminated water from sewers, irrigation systems, and factory waste. All backflow devices constitute internal springs, shut-off valves, seals, test cocks, and moving parts that experience wear and tear with age. To prevent water contamination and backflow, it is suggested to schedule professional inspection and maintenance at least once a year to nip any issue in the bud before they cause catastrophic damage to any vessel or system. Malfunctioning backflow preventers can allow hazardous contaminants such as bacteria, sediments, wastewater, chemicals, fertilizers, and pesticides to enter your drinking water.This is why it is necessary to take the maintenance and repair of backflow devices very seriously and look after any sewer pipe lining.
Table of Contents
Water Contamination
We expect the water coming out of our taps to flow unhindered, be clean and crystal clear, have a pleasant taste, and be odorless. However, contaminated water is usually the first sign of a malfunctioning backflow preventer. Contaminated water is usually discolored, sometimes brown, yellow, or even pink in color. The odor of polluted water resembles Sulphur (rotten eggs), and you may even notice rust particles or sediments floating in the water. Contaminated water has a distinct taste that is hard to miss. If your water ever shows signs of contamination, it needs to be dealt with swiftly before it poses health hazards. If sewer water mixes in with your drinking water supply, all pipes will need to be cleaned and sanitized before the water becomes usable again.
Faulty First Check Valve
The first check valve in a reduced pressure backup preventer opens up at certain water pressures, specifically a minimum of 2.0 PSI. This allows the water to then pressurize the space between the first and second check valves. However, a malfunctioning backflow preventer valve will open at much lower pressure or higher, impairing its function to allow water to flow only in one direction.
Faulty Second Check Valve
While inspecting the first check valve ensures that water is only flowing in the right direction, backflow testing for the second check valve checks for the possibility of backpressure. In case of a faulty second check valve, water can leak back into the area between checks, where it mixes in with contaminated water.
Noises
Check valves are known to emit noises as the first sign of trouble. We call this noise the “water hammer” and it is caused by the disc slamming into the seat of the valve. This phenomenon can lead to ruptured pipelines and severe damage. If you are experiencing this issue, try installing a faster-closing check valve to prevent pressure surges.
How to Protect your Backflow Valves from Malfunctioning?
Faulty valves can wreak havoc on systems and vessels. However, these measures can help you extend the life of each valve and avoid trouble.
Keep Valves Clean
Contaminants and debris can get stuck in the valve and cause damage to the internal mechanisms and eventual valve failure. Keeping your pipelines clean and preventing the buildup of debris is the best way to prevent failure. First things first, install filters and covers wherever needed to prevent any contaminants from entering the system. For any liquid systems, flushing the pumps between shutdowns helps to keep the pumps clean and prevent any debris from entering the system.
Lubricate Valves
Valves should be periodically lubricated as a part of preventive measures to optimize performance and ensure their proper functioning. Effective lubrication helps to elongate the life of each valve and prevent system failures.
Use Valves as Directed
The proper use of valves also ensures optimum operation and safety. for instance, it is necessary to make sure that each valve is correctly installed and assembled, and is of the right type and size for the application it is being used for. Installing the correct check valves prevent premature failures.
Replace Valves as Needed
Last but not the least, valves need to be replaced regularly to ensure longevity and prevent any valve damage or failures. If you notice any operation red flags or performance deterioration, it’s time to replace the faulty part with new ones immediately, before it leads to an ultimate system failure.
Hello, I am a professional writer and blogger at Adclays.com. I love to explore the latest topics and write on those topics. I spend the maximum of my time on reading and writing interesting topics which provide valuable piece of information to my readers whether it comes to the latest fashion, technology, healthy lifestyle, business information, etc. Explore my writings by visiting the website.