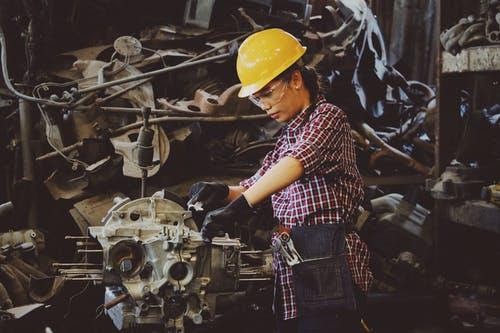
A company’s ability to run smoothly depends on more than just the production equipment and raw materials. It is important to maintain good facilities, transport equipment and production equipment, personal protective equipment inventory, and inventory for cleaning supplies, hand tools, and all other items.
Although these supplies and activities make up a small portion of a business’s operations, they can have an enormous impact on its bottom line. They account for only 5%-10% in product costs. Manufacturers could lose hundreds of thousands of dollars per day if a component used for equipment maintenance is out of stock and shuts down in a single day. Employee safety is at stake if PPE (Personal Protective Equipment) runs out.
Half of the items needed for Maintenance, Repair, and Operations are kept in storage for up to a year. This can lead to cash being held up in storage and could result in unnecessary waste such as batteries or materials that are not compliant with regulations. Before we get into the importance and definition of MRO, let’s first discuss what does MRO stand for.
Table of Contents
What Does MRO Stand for?
MRO stands for maintenance, repair, and operations. This term refers to the entire set of activities and operations involved in the maintenance and repair of a facility or structure. It can include the physical maintenance and operation of the building or structure, the system that operates within the facility, and the equipment that produces the primary business output.
The Importance of MRO Maintenance
MRO data maintenance is a must-have for any engineering or manufacturing company. MRO relies on thousands, if not hundreds, of components. This demands a reliable and up-to-date data management system, which must also be maintained.
MRO stands for maintenance, repair, and operations. This refers to the fixing, repair, and maintenance of electrical and mechanical systems and devices. MRO maintenance is crucial to the efficient running of any company that involves manufacturing or engineering systems. This includes repairs to broken or faulty machinery and routine maintenance programs that help prevent them from happening.
For the smooth operation of these systems, it is essential that accurate and current data records be kept. This includes an internal catalogue of parts and auxiliaries with current information about suppliers. You need to be aware of when a part you use is going out of date so that you can stock up on it or find a new one. Part obsolescence management is also essential.
It’s easy to forget about these things when running a busy business, especially if your MRO data system is not working correctly. This is where MRO maintenance services companies are here to help. MRO maintenance services and data cleansing solutions will ensure an efficient method of optimizing and managing your MRO materials data. This can be achieved with a single catalogue that consolidates all parts and materials used in your system.
MRO Inventory Best Practices
These MRO inventory management tips will help anyone looking for the best MRO inventory practices.
Define The MRO Inventory Items Which Are Most Important to Your Business.
MRO has some things; if they are missing, that will not cause a business to go out of business. Others might. These items can be identified along with their usage rates and minimum reorder points. Do not allow the replenishment of these items to slip by, no matter what you do.
When purchasing MRO inventory, consider the whole organization. MRO products may be needed for different teams within your company. Take a look at the needs of each team and identify areas where efficiency can be achieved or bulk-order discounts.
Speak to Suppliers About VMI Arrangements.
You can outsource inventory management to trustworthy suppliers or look into hybrid MRO options. Like many survey respondents, you may discover that employees are more productive when MRO inventory management runs smoothly. This allows your company to focus on its most important business goals.
Use Demand Forecasting and Analysis.
Forecasting MRO inventory is not intuitive since there is no buyer demand. MRO inventory management, as with all successful inventory management strategies, depends on demand forecasting. You can determine when you have high and low demand seasons and adjust your replenishment accordingly. Set key performance indicators (KPIs), such as stock outs, on-hand inventory, and replenishment points, and be consistent with them.
All MRO Inventory Should Be Kept in One Central Location.
The central stock area can then be audited using computer systems to track all inventory. This encourages the use of computer systems to track and control inventory and discourages private inventories. This is one of the best MRO inventory practices we have seen.
Your Staff Should Be Educated About Supply Chain Management.
Many companies who keep MRO inventory control in-house use manufacturing staff to manage it. To increase their knowledge and control your MRO inventory, you can teach them about transit inventory and supply chain management.
To Ensure That Your MRO Inventory Is Not Bloated, Conduct A Quarterly Audit.
MRO inventory changes and grows as production methods change. Your production methods change based on many factors, including current technology, demand, location, and raw materials inventory. There will always be some MRO inventory you don’t need, or that isn’t needed in the order quantities.
Final Words
If you can do all these, you will be optimizing a portion of your business that many companies don’t even think about. This is a competitive advantage.