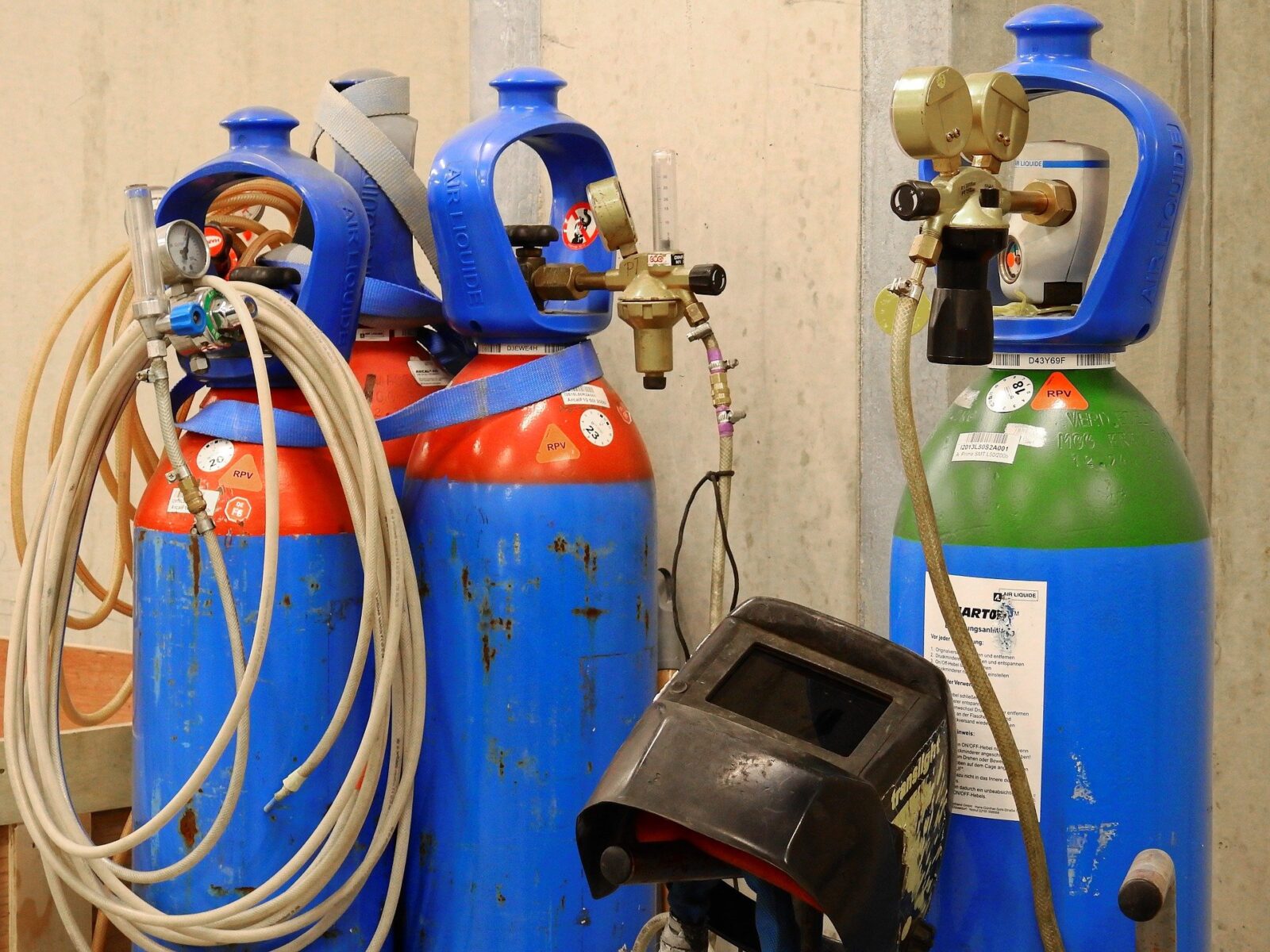
Australia sees a high demand for welders annually. A profession that requires the technical skills to carry the industry, weldors see themselves rapidly innovating to the latest technology. At a time when Welding gases became a prized commodity of the industry.
The different types of gases and cryogenic liquids are exciting to work with, thanks to their myriad chemical properties. However, understanding the right volume and frequency and extracting it using the correct device is crucial to a welding job. With the right supplier, procuring welding gas will no longer be an occupational hazard.
HOW TO USE GAS?
Compressed gas and cryogenic liquid are widely extrapolated for industrial, healthcare and speciality sectors. Welding is not the only industry functioning on gas.
Manufacturing, laser cutting, food, beverage, pharmaceutical and laboratory sectors rely on the application of gas to get their products running. The gas required could be common or rare. It might be needed in a single cylinder or gigantic vessels. Ensuring that the gas is per the Australian Government’s license requirements is paramount to avoid any potential risks. In addition, a supplier will have in-house chemical testing services and accreditation to show its quality.
PPE kits and safety manuals are issued to the workers handling these materials. The dangers of each gas vary, and there is no one manual for all. Safety training is a must for anyone coming into close contact with gases. This is keeping in mind the security of everyone involved.
Minimizing the environmental impact is as important as the distribution of gas. Holding sustainable standards is key to creating an industry that places environmental pollution as a crisis in its business strategy.
THE CHEMISTRY BEHIND WELDING
There are two types of gases common in welding. They are inert and reactive gases. Self-explanatory, inert gases provide stability to welding without interference from foreign elements. Reactive gases, on the other hand, alter the material to enhance the features during welding.
Often thrown around in welding literature are shielding gas, purging gas, heating gas and blanketing gas. Understanding these terminologies can help in breaking down the science of welding technology.
SHIELDING GAS
Machine welding is impossible unless a shielding gas is involved. The gas used for this purpose is inert and hence making it a contaminant-free zone. It will also prevent air bubbles from colluding to create an irregular weld. Inert gases come sans colour, odour or reactive properties. Yet Argon, Helium, Hydrogen, Nitrogen, Oxygen and Carbon Dioxide are used alone or to prevent any hindrance to welding quality.
PURGING GAS
Similar to shielding, purging gas is used to protect the material that is being welded. The inert gas unleashed into the apparatus can put off an inflammable reaction from happening. Purging is done separately using gases like Nitrogen and Carbon Dioxide predominantly.
HEATING GAS
Used in both hand welding and speed welding, hot gas is made for a manual welding process. The metal can be softened or warmed using fuel mixed with oxygen.
BLANKETING GAS
Blanketing comes after the welding gas is completed. The tank or enclosure are susceptible to foreign particles. So to avoid reactions, blanketing gas is added.